A non-functional Dyna Myte 2400 milling machine was donated to the Robot Garden makerspace in Livermore, California. The Dyna Myte 2400 was built in the 1980’s and its retrofit presented some unique challenges. Robot Garden was unable to get it going in a previous retrofit attempt. The machine sat in storage until it was revived using a Buildbotics CNC controller.
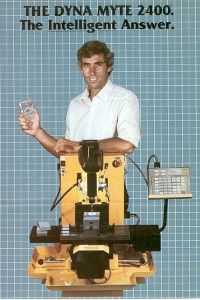
Robot Garden was delighted when Buildbotics offered to revive the Dyna with their new Open-Source CNC controller. The Dyna retrofit demonstrates some of the power and flexibility of the Buildbotics controller. For instance, the stepper motors on the Dyna only provide 27 ounce-inches of torque. The original machine compensated for this low torque by providing a 10 to 1 gear ratio between the motor and the axis ball screws. Given the 2.5 mm pitch ball screws, the machine head would only move by 0.25 mm for each complete revolution of the motor. In order to meet the published jogging speed of the machine (30 IPM), the stepper motors had to turn at 3000 RPM. The controller had to provide over 5000 steps per second to minimally meet that goal. This was a breeze for the Buildbotics controller which is capable of over 200k steps/sec. Performance was further improved with 1/32 micro-stepping. The resulting 160k steps/sec yielded smooth, reliable operation.
Subscribe to the Buildbotics mailing list.
Buildbotics also supplies a cable set that made interconnecting to the existing motor and power supply a snap. An enclosed I/O breakout box was used to connect to the existing spindle controller and the limit switches. Finally, a couple of shelf brackets from the local hardware store provided a nice mount for the controller.
This previously unusable Dyna Myte 2400 is now a solid CNC mill with modern features and should provide great service for years to come.
The Buildbotics controller generates its own steps and contains a web server, so you don’t need to dedicate a PC; and you can configure and control it across your local Ethernet using a web browser. Eliminating the PC cuts costs and saves space.
The Buildbotics CNC controller can operate on voltages from 24 to 48 DC and supply up to 6 amps of current on each motor, but no more than 25A total. Smooth S-curve acceleration and deceleration allows machines to operate without sudden changes in acceleration which cause jerk. The ability to provide local jogging control with an inexpensive USB gamepad and to monitor cutting remotely through a USB web camera is also really handy.
The hardware and software for the controller are completely Open-Source and work directly with CAMotics. CAMotics is an Open-Source simulator, GCode viewer and CAM software. After simulating designs, CAMotics allows its users to connect directly to the Buildbotics CNC Controller and upload GCode programs. CAMotics will follow the cutting operation in real time. This lets you easily see where the machine is in the cutting process an how long it should take to complete.
This range of performance and features make the Buildbotics controller ideal for controlling a variety of CNC machines. Buildbotics has demonstrated control of several different CNC machines including the OX, the Taig Mini-Mill, a 6040 CNC, an engraving machine, a LASER cutter, and a sizable DIY CNC.
You can get your own Buildbotics CNC controller and support this great Open-Source project through the Buildbotics store. For detailed instructions on how to perform this retrofit check out our hackaday.io project.